Restorations Done Right
We use an industry leading 3 stage process to evaluate and repair your pump. Our experienced machinists and engineering team specialize in diagnosing and repairing both dynamic and displacement pumps. If the proper repair requires any parts that are hard to find or out of stock, we can fabricate them to precise specifications to ensure that every repair meets original design and performance standards.
Full Pump Restoration Process
For experienced pump repair technicians, achieving durable and reliable repairs is a straightforward process. Similar to other maintenance procedures, it relies on: diligent monitoring for anomalies, meticulous record-keeping, the utilization of high-quality replacement components, and a thorough attention to detail.
While it might be appealing to imagine proprietary techniques that guarantee exceptional repair outcomes, the reality is that consistent quality work and a focus on precision in every aspect are the fundamental determinants of success.
At Southeast Texas Pumps, we follow a robust process to ensure that each pump rebuild exceeds our client expectations.
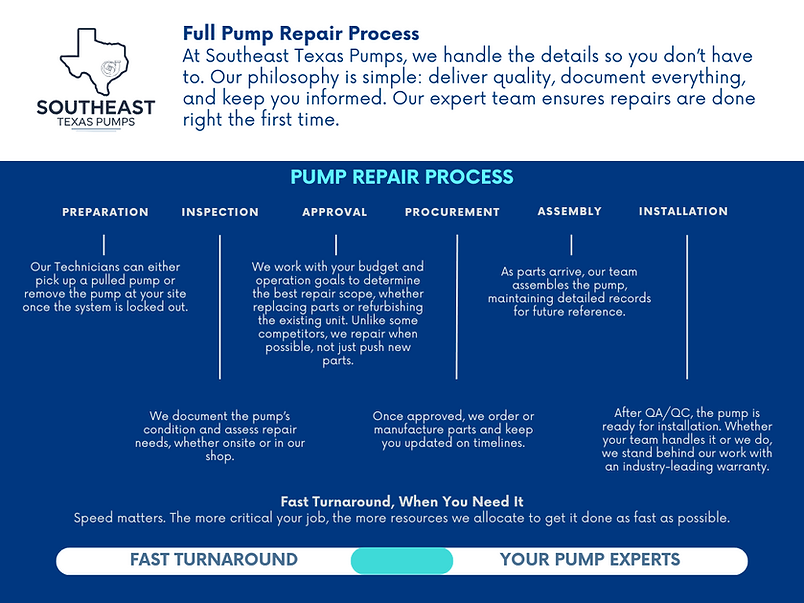
Disassemble, Clean, and Inspect (DCI)
The Disassemble, Clean, and Inspect (DCI) area is a critical zone in the pump repair workflow. This area is dedicated to disassembling incoming pumps, cleaning components, and conducting thorough inspections to determine the repair or replacement needs for each part. By effectively diagnosing the issues, this area ensures that repair or replacement work is performed accurately and efficiently.
The DCI area forms the foundation for the repair process by ensuring that every pump entering the facility is properly assessed and prepared for subsequent stages. So many shops skip this step, but if there is a pump coming in, especially if it is a troubled actor, paying attention to how it is received is the only way for the pump to tell you its history. Skipping this step makes it significantly harder to identify why things are going wrong. Here are some key questions we use to investigate each pump:
Was the coupling worn out of round due to improper DBSE, broken shims, or was it a different installation issue?
Did the seals fail early due to lack of seal fluid, incorrect parts or some other installation issue. Do we know if the bearings were running hot and if so how hot?
Was it an alignment issue with the pump and driver, piping or some other installation issue?
Whatever the reason for the repair, a thorough Disassemble, Clean, and Inspection (DCI) following a set process with detailed notes is the best way to hear what the pump is saying. Therefore, we have an entire area dedicated to disassembling incoming pumps, cleaning components, and which has all the precision instruments needed to conduct the thorough inspections to determine the repair or replacement needs for each part. The DCI area forms the foundation for the repair process by ensuring that every pump entering the facility is properly assessed and prepared for subsequent stages.
Workflow Steps
Pump Intake - The pump arrives, and the job number is assigned. The pump is assigned to a specific storage “spot” so that all the parts and bits are kept together and available for outside inspection at any time.
Initial Documentation - Basic details are recorded, and the pump is photographed for reference. The as-received condition is thoroughly documented following our detailed procedure to ensure that commonly needed information is obtained prior to it being lost forever after the pump is disassembled.
Disassembly – Qualified technicians disassemble the pump, using specialized tools to avoid damage to components. During this process we are careful to verify that the condition of parts as we remove them and verify that previous installation was as expected with parts appropriate for the pump and service.
Cleaning - Components are cleaned using appropriate non-destructive methods. All too often we have remanufactured parts from rotating equipment that were “cleaned” with an angle grinder.
Inspection - Thorough inspection is conducted, and findings are documented. This includes the verification that all of the seales, bearings, sleves, shafts, etc are the appropriate ones for the service, the ones specified by the OEM or the customer and within acceptable tolerances. Any deviations are noted.
Tools
While tooling might not traditionally be categorized as a direct DCI (Define, Collect, Improve) process, its meticulous application is integral to our high standards. Consider instances where "as-received" parts exhibit damage inconsistent with normal operation, such as a mushroomed pump shaft end, strongly suggesting forceful removal. Our approach prioritizes the preservation of component integrity from the outset.
Removal Tools: Leveraging two decades of pump repair expertise, we employ a comprehensive suite of removal tools, including bearing pullers, hydraulic presses, and custom-designed fixtures. This ensures the disassembly of each assembly with minimal destructive force, a process thoroughly documented at every stage.
Inspection Tools: Recognizing that specified tolerances for pumps and compressors often fall within the thousandths of an inch, we utilize calibrated precision instruments for component inspection. This includes depth gauges, calipers, micrometers, and dial gauges, guaranteeing that all removed parts are assessed against stringent specifications, a level of accuracy unattainable with basic measurement tools.
Root Cause and Repair Scoping
After the DCI stage is completed, our comprehensive DCI documentation package contains data about the pump parts that are:
Within specification and just need to be cleaned, polished and reused.
Need replacement and are readily available for purchase and can be ordered and obtained within the timeframe of the repair
Need custom manufacturing or modification.
Using this data, our senior staff then develops a repair strategy aligned with the customer's budget and schedule goals. We review and discuss the repair plan, timing, and cost with the owner prior to initiating any work. During the review, our experts present any alternatives with associated life cycle cost and operations impacts if applicable. This allows the customer to make an informed decision on the path forward considering all of their options given the constraints of budget and time.
Workflow Steps
Specifications & References: Relevant technical specifications, including drawings, manuals, and standards (OEM, engineering, internal, or customer-specific like API), are compiled to define material requirements, dimensions, tolerances, and applicable standards for all repair or replacement activities. The aim is to meet or exceed OEM specifications unless otherwise approved.
Root Cause Analysis: The pump's condition and disassembly notes are analyzed by experienced personnel (e.g., Quality Manager, engineer) to determine the underlying reasons for failure (e.g., normal wear vs. improper lubrication or cavitation). Identifying the root cause ensures that corrective actions address fundamental issues, preventing recurrence.
Define Repair Scope: A comprehensive list of required actions is generated based on inspection data, detailing parts to be replaced, repaired/refurbished, and those in good condition. Necessary machine shop operations and a preliminary list of parts and materials to order are identified. This defines the official repair scope, requiring customer approval for any deviations from the initial expectations or quote.
Resource Planning: The availability of necessary resources (machinery, tooling, calibrated instruments) and personnel qualifications (e.g., certified welders, experienced machinists) is verified for each repair step. Subcontracted processes (e.g., heat treating, balancing) and their quality verification methods are also planned.
Repair Plan Documentation: The detailed repair plan is documented, outlining tasks step-by-step with associated quality control (QC) checkpoints integrated as operations (e.g., machining with dimensional QC, welding with NDT and machining QC, assembly with clearance checks). This ensures process quality control throughout execution.
Timeline and Responsibilities: An estimated timeline is established, and responsibilities for each task and QC verification are assigned, typically coordinated by the Production Supervisor. Critical steps may require the presence or sign-off of the Quality Manager or QC Inspector.
Customer Communication: The repair plan is communicated to the customer, especially regarding significant changes in scope, cost, or timeline. Obtaining written customer approval for the final repair scope ensures alignment and prevents non-conformances.
Tools
Since we have a fully integrated machine shop, we can scope and propose reverse engineering and manufacturing of replacement parts faster than could be obtained through the original equipment manufacturer. In some cases, re-engineering obsolete parts may be the only option to keep an obsolete but effective piece of equipment running.
Reassembly
Once we have a go-ahead on the proposed repair scope, we:
Reverse engineer and manufacture parts
Obtain replacement parts
Modify/repair existing parts
We then start the process of reassembly. The pumps are put back together in an area custom designated for reassembling pumps. This area is a critical space where repaired or replaced components are re-installed back into the pump. As with disassembly, we use the proper tooling to ensure that each tolerance is properly set and measured and documented. This help ensures the proper functioning of the repaired pump through adherence to manufacturer specifications. Using these methods we have significantly lower returns than many of our competitors.
Workflow Steps
Component Staging - All components required for reassembly are gathered and verified to ensure they are the correct parts and meet the customer or OEM specifications.
Sub-assembly - Smaller components are assembled separately, such as seals or bearing housings. We verify that these smaller assemblies meet tolerances and specifications (e.g. concentricity) and have found that this is imperative to ensure that the final pump assembly can pass all of the specifications and OEM alignment and vibration requirements.
Main Assembly - The main pump body is reassembled using appropriate tools and alignment techniques. So many times have we seen pumps assembled with impact drviers. Not at SouthEast Texas Pumps, we do things using hand tools and torque wrenches to ensure that each bolt is installed with the perfect amount of force.
Seal Installation - Gaskets, O-rings, and mechanical seals are reverified to ensure that they are correct for the pump. We then follow the manufucturers recommendations and install each seal, with proper tools and ensure proper alignment and seating.
Alignment and Calibration – Once all the components are together we follow our comprehensive aligned reequipments and ensure that the pump is aligned and calibrated according to specifications.
Tools
Lifting Equipment - Hoists, cranes, or forklifts to safely move heavy pump components.
Alignment Tools - Laser alignment tools or dial indicators to ensure proper alignment of components.
Seal Installation Tools - Specialized tools for installing gaskets, O-rings, and mechanical seals.
Compressed Air System - For cleaning components and ensuring debris-free assembly.
Lubrication System - Equipment for applying grease or oil to bearings, seals, and other parts requiring lubrication.
Calibration Equipment - Instruments for calibrating components to ensure proper operation post-assembly.